What is a bill of materials (BOM)? Examples and software for automation
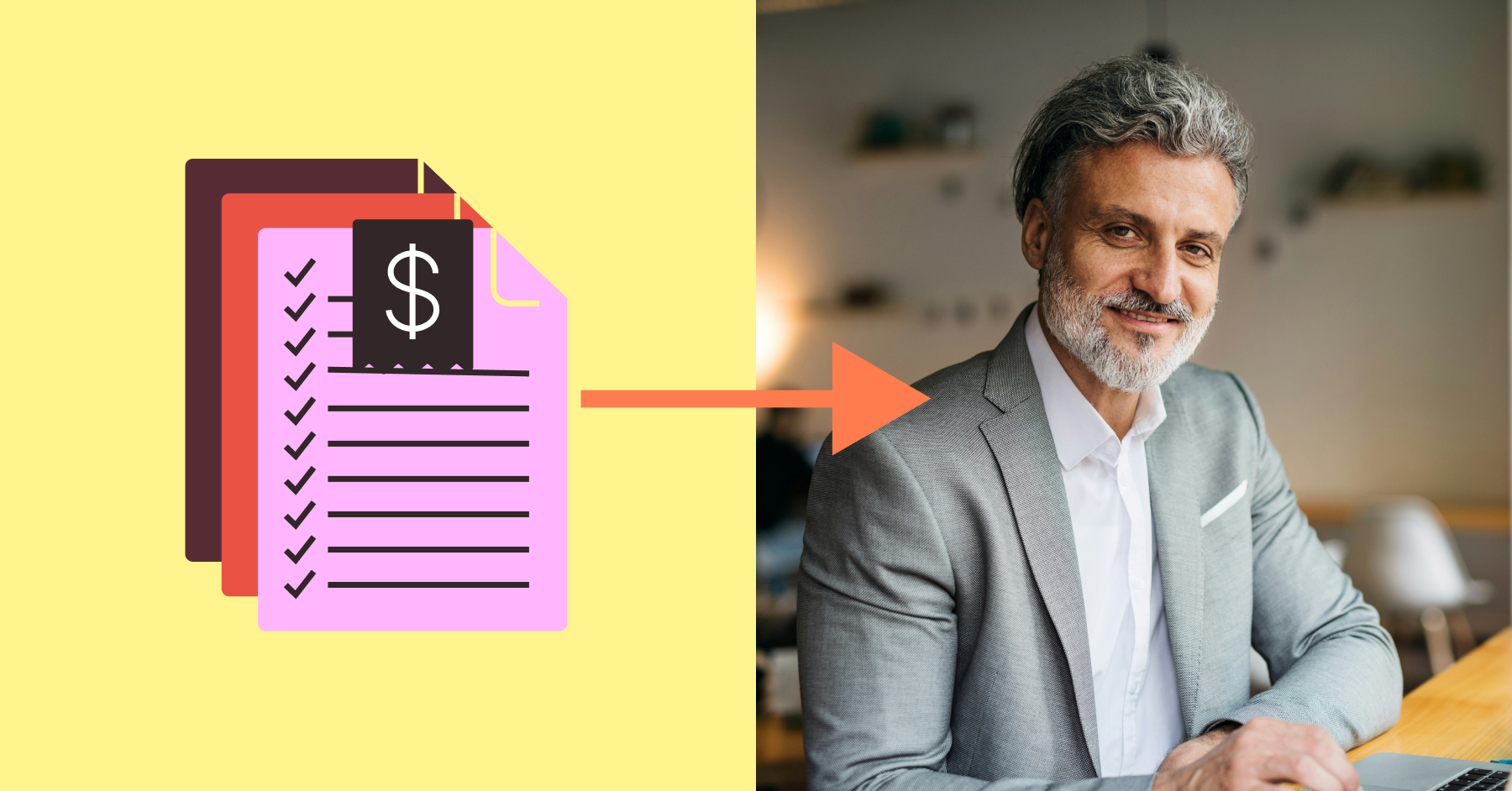
The bill of materials (BOM) has become a foundational piece for supply chain managers and operations directors trying to drive efficient production and manufacturing.
A bill of materials is typically relied on to facilitate efficient procurement, production, and inventory and supply chain management.
Below, we’ll dive into what a bill of materials is (with examples), how it works, challenges, and how you can automate the BOM process.
What is a bill of materials?
A bill of materials (BOM) is a comprehensive document that highlights a detailed roadmap of what is needed, and what needs to be done to manufacture a product.
BOMs often include exhaustive specifications, including:
A well put together bill of materials requires meticulous attention to detail.
When done right, however, a BOM serves as a linchpin in the manufacturing lifecycle of any individual product.
What makes BOMs important?
The impact of a bill of materials can be felt across the entire supply chain.
A BOM is instrumental in optimizing operational efficiencies and ensuring product accuracy and consistency. This helps you better control costs and stay on efficient schedules.
By understanding procurement and production timing, you can better plan and forecast the purchase of raw materials and other foundational components. This gives you a cleaner window into cost estimations.
You can also optimize the quantity of materials needed, effectively reducing production waste.
When the manufacturing process is delayed or fails, a bill of materials serves as a record of production, making it easier to backtrack and identify the exact point in which the supply chain was broken.
Bill of materials impact on cost of goods sold
A bill of materials is also an essential piece in calculating cost of goods sold (COGS).
Cost of goods sold includes only costs directly related to procuring and making products. That entails raw material cost, manufacturing cost, packaging, shipping and freight, and the related labor costs.
In other words, it’s your BOM, plus labor and shipping costs per unit of inventory.
While the lines can be blurred depending on the exact service or product being offered, generally, COGS will not include tangential costs like marketing, sales, distribution, and other administrative expenses.
Calculating COGS can be done using the following formula:
COGS = Beginning Inventory Cost + Purchased Inventory Costs - Ending Inventory
Accurately calculating cost of goods sold is critical for knowing the true cost of producing your merchandise.
BOMs serve as a critical factor in calculating COGS, setting product prices, and forecasting potential spend and revenue.
Who benefits most from using BOMs?
The companies that typically benefit most from using BOMs are those that need to keep a close eye on the cost of manufacturing a large inventory of goods.
Why?
It’s typically more relevant and doable for larger companies to rely on BOMs, given the volume at which they manufacture products, and the bandwidth required to calculate, understand, and draw insights from COGS, profit margins, and other revenue impact factors.
Within these companies, supply chain managers, procurement, and manufacturing teams are the main teams that stand to benefit from a bill of materials.
That said, various departments and stakeholders across the supply chain get use from BOMs.
Engineering and design teams utilize BOMs (or EBOMs) to ensure that designs align with the availability of materials and required timing of production.
Quality control teams refer to the BOM to verify that the right components are used in the right order throughout the production process.
In some cases, especially for more complex or customizable products, sales and marketing teams may actually refer to a BOM to understand intricacies and nuances they may want to relay to customers.
A bill of materials is also a useful document for any stakeholding decision-maker. Board members, investors, and internal management can use information present in BOMs to understand supply chain performance and inform go-forward strategy.
Bill of Materials Example
As an example, here’s a stripped-down version of what a bill of materials might look like for a chair:
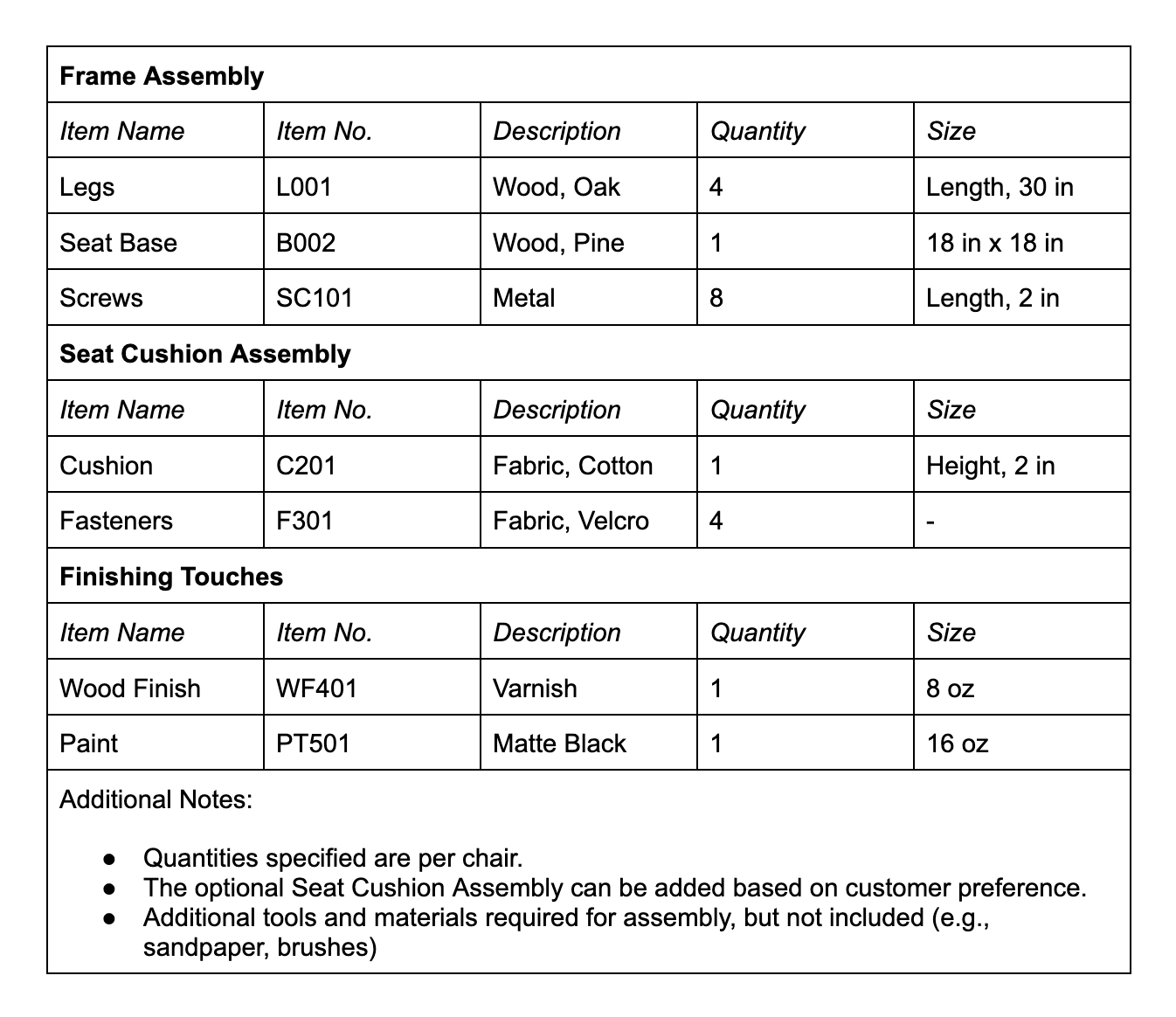
Sample image of bill of materials for a chair
Bill of materials templates
A quick web search allows you to find a variety of different BOM templates.
Depending on your need, you can also specify the kind of template you need, whether that’s for Excel, Google Sheets, etc.
A few websites currently offering bill of materials templates are:
Bill of materials management challenges
Assembling and managing a bill of materials can be challenging due to the volume of data required, and the disparate sources in which that data comes from.
Without the right software and processes in place, it can become incredibly time-consuming to manage BOMs across your entire inventory.
Lack of data standards
Each product is made up of a multitude of different components. Each of those components likely comes from a different supplier, on different timelines, with different units of measurement, and different overall data standards.
That can create an immense body of work for your team to standardize all of that data across each individual product.
Additionally, since this information is coming from so many disparate locations, it can be difficult to centralize all of that into one place.
Let’s refer back to our chair as an example…
Above, the bill of materials example may look fairly simple and straightforward. Broken down by its components, however, you can see how disparate the data would be.
To get to the final example above, you’d have to centralize and standardize all data from your wood supplier, metal supplier, fabric, paint, and so on.
Volume and granularity of information
On top of that, the amount of information needed to assemble BOMs is quite large.
Sourcing teams, for example, may need to manage a bill of materials that ties back to the SKU of each individual product, inclusive of all relevant manufacturing data.
While brick and mortar stores may only have a few thousand SKUs on-hand, e-commerce companies may have hundreds of thousands of SKUs.
It goes without saying, but managing this many BOMs is a massive feat.
Manual, time-consuming processes
Most companies rely on Excel to manage their BOMs.
The problem is that there’s no inherent way within Excel to automate the centralization and standardization of all the involved data.
Unless you have a developer on-hand building automations via VBA, you’re typically required to copy and paste data from all of your vendors and manufacturing partners into one place, and format that data yourself.
Not only is this time-consuming, but it’s likely (and natural) to be error-prone.
How to simplify the bill of materials management process
Managing a bill of materials is essential for efficient production and operations. With Parabola, you can streamline and optimize the BOM management process to save time and reduce errors. Here’s how:
1. Streamline the bill of materials management process
Parabola simplifies workflows for bill of materials management, allowing you to integrate data from multiple sources. This ensures your BOM stays accurate and up-to-date, reducing inefficiencies across your production cycle.
2. Enhance operations with BOM software
Pair Parabola with your existing bill of materials software to automate tasks like data consolidation and reporting. With Parabola, you can take your BOM management to the next level by building custom, automated workflows tailored to your needs.
3. Track and improve the BOM management process
Gain real-time insights into your bill of materials in supply chain management with Parabola’s automation capabilities. By identifying discrepancies and tracking changes, you can make smarter, data-driven decisions.
4. Visualize your bill of materials example in action
Parabola helps you create and analyze a bill of materials example with ease. Whether it’s a single product or a complex assembly, you can map out every component to ensure your operations run smoothly.
5. Optimize your supply chain with better BOM management
By automating your bill of material management process, Parabola helps you reduce delays and improve collaboration. From small businesses to large enterprises, an efficient BOM management process is key to supply chain success.
With Parabola, managing a bill of materials becomes simple, efficient, and scalable. Whether you’re using advanced BOM software or need a flexible tool for automation, Parabola empowers you to streamline your bill of materials management process and focus on what matters most: delivering exceptional products.