What is your freight audit process missing?
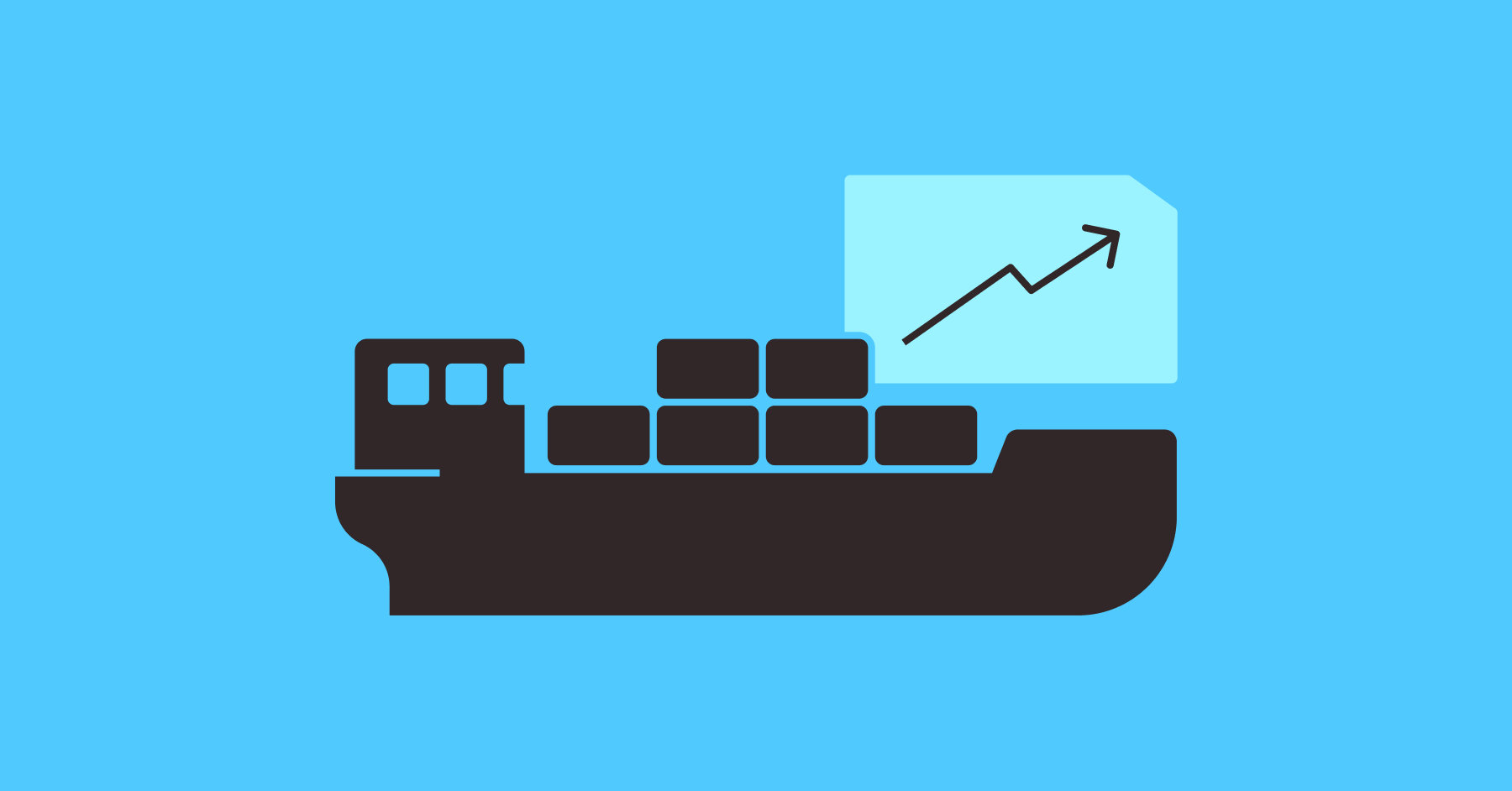
Freight audit and payment involves reviewing carrier invoices to prevent overcharging on shipping costs, demurrage, and other fees. This process has become increasingly challenging as companies manage thousands of invoices across various formats, from PDFs to spreadsheets, with error rates reaching significant levels due to fragmented data sources and legacy systems.
The main challenges include complex freight contracts with variable expenses, incomplete shipment data, and time-consuming manual validation processes. Traditional approaches often require skilled employees to spend valuable time on tedious verification tasks instead of strategic work.
Parabola transforms this process by automating invoice validation and data integration across multiple sources. The platform can seamlessly connect PDFs, spreadsheets, and transportation management systems, automatically comparing actual costs against rate cards and identifying discrepancies. This automation not only reduces labor costs and processing time but also improves accuracy in catching billing errors, ultimately leading to better cost recovery and more reliable shipping data for strategic decision-making.
What is a freight audit?
Simply put, freight audit and payment is when a shipper reviews a freight invoice from a carrier to ensure they aren’t overcharged. In this process, the shipper conducts a freight bill audit for trucking and air shipping costs, demurrage, and more, comparing the actual cost to the estimate on a rate card provided by the carrier so they can recoup any charges they don’t owe.
What makes the freight audit process so challenging?
Because freight audit requires managing thousands of freight invoices that come in all different formats, the process of standardizing and preparing invoices for a shipping audit is extremely tedious and time-consuming. The shipping data lives in emails, spreadsheets, and PDFs with non-standard columns, sections, and headers — and getting it all into one place is a headache, to say the least.
Each complicating factor in the freight audit process is worth solving for one reason alone: the opportunity for cost savings.
Error-prone freight invoicing processes
Why is it that such a high number of freight bills have errors that cost importers of record millions of dollars each year?
Many companies that use legacy transportation management systems have been around for decades — some freight companies haven’t updated their systems since the dawn of transportation management systems in the early 90s. Fragmented data sources like spreadsheets, email, and PDFs, and lots of manual work all contribute to a less-than-streamlined process — and before now, there have been few solutions to combat this.
And because all of the touchpoints involved (PDF freight invoices, rate cards in emails and spreadsheets, TMSes, and more) aren’t built to work together, data often gets lost in translation. This happens in countless ways — for example, the same line item may be defined or categorized differently by different carriers, even though they’re the same thing (i.e. “trucking wait fee” vs. “per diem”). Even for modern freight companies, optimizing the flow of data so that it can be trusted, requires work and buy-in from the entire organization.
A fundamental lack of trust in data means that companies are often unable to accurately forecast landed costs. If they don’t pay carriers and other partners within their negotiated terms, they risk facing big penalties.
To avoid facing penalties, shippers are forced to spend hundreds of thousands of dollars a year allocating valuable employee time to validating freight bills and rate cards manually, and they’re still not able to get trustworthy outputs. Outsourcing this work isn’t a viable option either, because it costs just as much and provides even less visibility into essential data.
Freight contracts that are too complex
The way shipment costs are calculated isn’t cut and dried. There are highly variable expenses like fuel surcharges, accessorial charges for services beyond pickup and delivery, surcharges for any value-added services like palletization, sort and segregation, or dedicated trucks for changing delivery locations, and more. Some carriers have rate cards with multiple calculation methods for their various freight lanes. For example, ocean shipments moving on the same lane may have either a fixed rate or a spot rate, and rates can vary. With thousands of shipments and transport invoices to validate during freight audit, these calculations get hard to keep track of very quickly.
For businesses with particularly complex supply chains (like companies selling perishable goods), the shipping audit process has to reflect these complexities: they need to use warehouses and shipping partners who have access to the right storage facilities to keep things fresh. Not only do these retailers need to diligently track and trace every step of the shipping process, but they also incur added costs for refrigeration as well as special packaging and insulation.
When you’re doing this process manually for hundreds or even thousands of shipments, regardless of what you’re shipping, it’s incredibly complex — not to mention error-prone and time-consuming.
In a freight audit, the shipper needs to figure out exactly what each charge was for, and understand every surcharge and shipment cost calculation method. If they’re lucky, the carrier will make the process easier by providing information about each charg — but that’s not always the case.
Absent or incomplete shipment data
Data loss is inevitable when validating and combining thousands of shipments through multiple systems. Without complete and comprehensive shipment data, the shipping audit process can be painfully long and manual. During a freight audit, you may spend days trying to find the root cause for late deliveries or service issues, because like with added costs, the carrier likely isn’t going to volunteer that information to you.
Some shippers who are stuck with their legacy systems are forced to make educated assumptions about the status of a freight invoice or what’s included on a rate card. Not only does this add a lot of work up front to verify information, but it adds more time and cost on the other end: either the claims process will be held up because your information is incorrect, or worse, you’ll never even find out about overages that you’ve paid because they got lost in the shuffle.
How the freight audit process can be improved
Manually managing the inner workings of a freight audit and payment process is a huge undertaking — and doing it with 100% accuracy is nearly impossible. By removing the manual aspect of the workflow through automation, you stand to see significant time and labor cost savings, and your data becomes way more trustworthy.
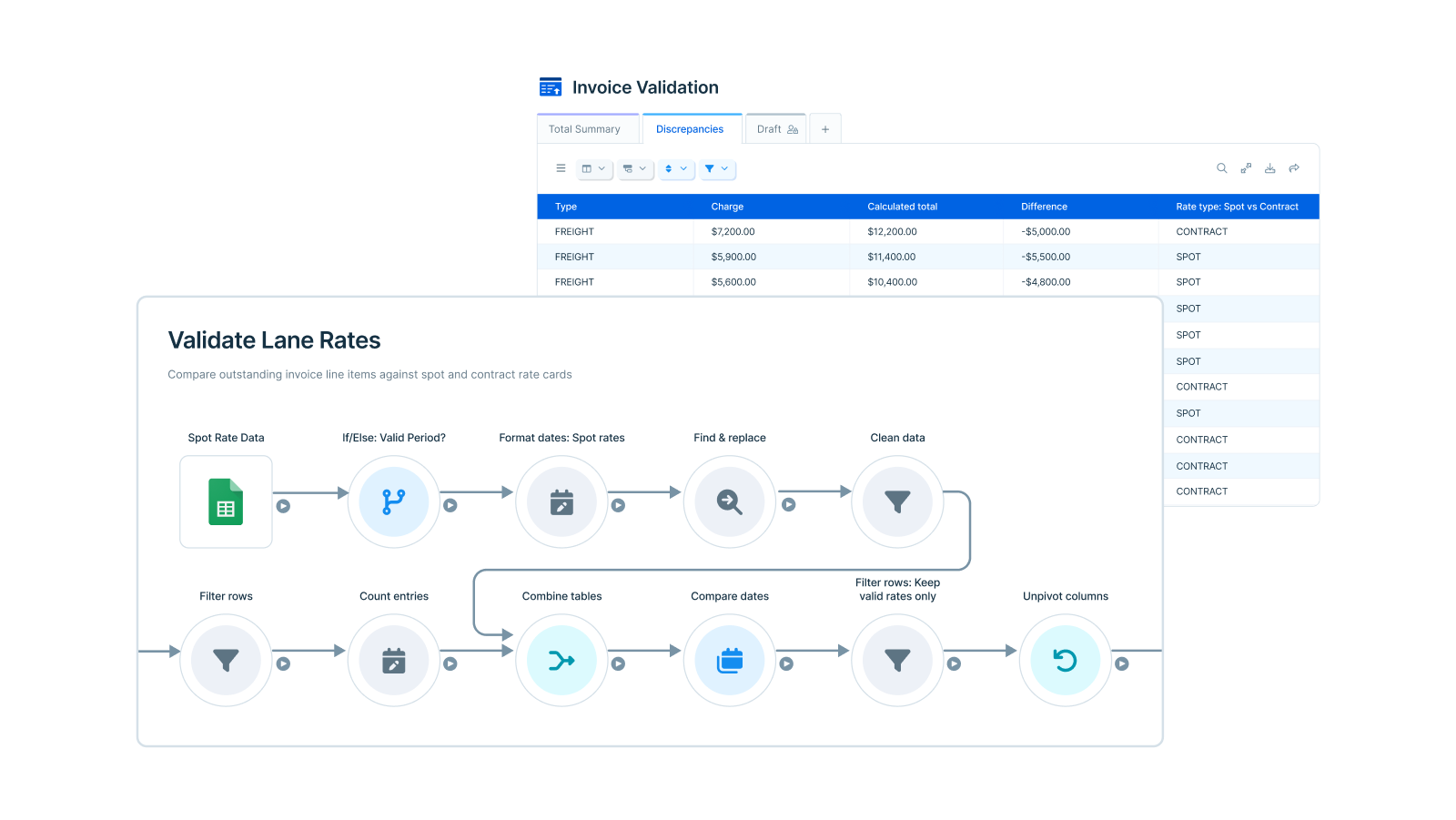
Example snippet of an invoice validation flow
Saving time and costs
No manager wants to hire a team of skilled people only to have them responsible for managing freight audit workflows that shouldn’t have to be done manually — and that should run on their own. The amount of employees’ time that must be spent verifying invoices adds up to massive opportunity cost. Not only that — it also means that no one has the time to do the jobs they were actually hired for, because they’re too busy keeping freight audit processes afloat.
By automating your freight bill audit process, you can eliminate manual processes like uploading data into your TMS, comparing actual shipping costs against a rate card, and submitting claims for overages. You can allocate less money toward labor, and by removing manual work, you’ll also catch more invoicing errors and recoup more of the costs you don’t owe.
Improving data integration
Automating your freight audit drives precision. When you automate freight audit, you’re ensuring that each point in the process works infallibly with the next.
For example, with Parabola, you can integrate any system and data source you’re already using — whether it’s an emailed PDF, Google Sheet, Looker, or a TMS — so they work together seamlessly to generate accurate shipping cost reports. It’s also incredibly easy to update the workflows you build, so if your rate card or another part of your process changes, it takes a few minutes to adapt across your entire workflow.
Trusting your shipping data not only makes freight audit go faster from invoice preparation to the claims process, it also allows for better decision-making. With automatic data discrepancy resolution, analysts can trust that the data they’re looking at is correct and up to date. And they can actually focus on their expertise — optimizing logistics and allocating resources more effectively — to improve profitability.
The freight audit and payment process is essential, but it shouldn’t be a headache. To learn about how to get back the time your team is spending on the freight audit process and how you can better trust your data, set up some time to chat with our team.
Freight invoice automation with Parabola
Parabola transforms your freight and parcel audit processes by automatically ingesting data from carrier CSVs, PDFs, and third-party portals, then compares that data against rate cards to find overages or inaccurate charges. With most carriers providing only 30-60 days to submit a dispute, audit velocity is key for any team shipping at scale — and auditing in spreadsheets leads to human error, unscalable process, missed savings, and limited visibility into billing discrepancies across carriers.
Beyond reconciling values like parcel rates and fuel surcharges, Parabola can also audit more complex values like accessorial fees, weight and dimensional charges, service level failures, and volume-based discounts. Even if your rate cards and invoice PDFs are totally unstructured and lack standardization.