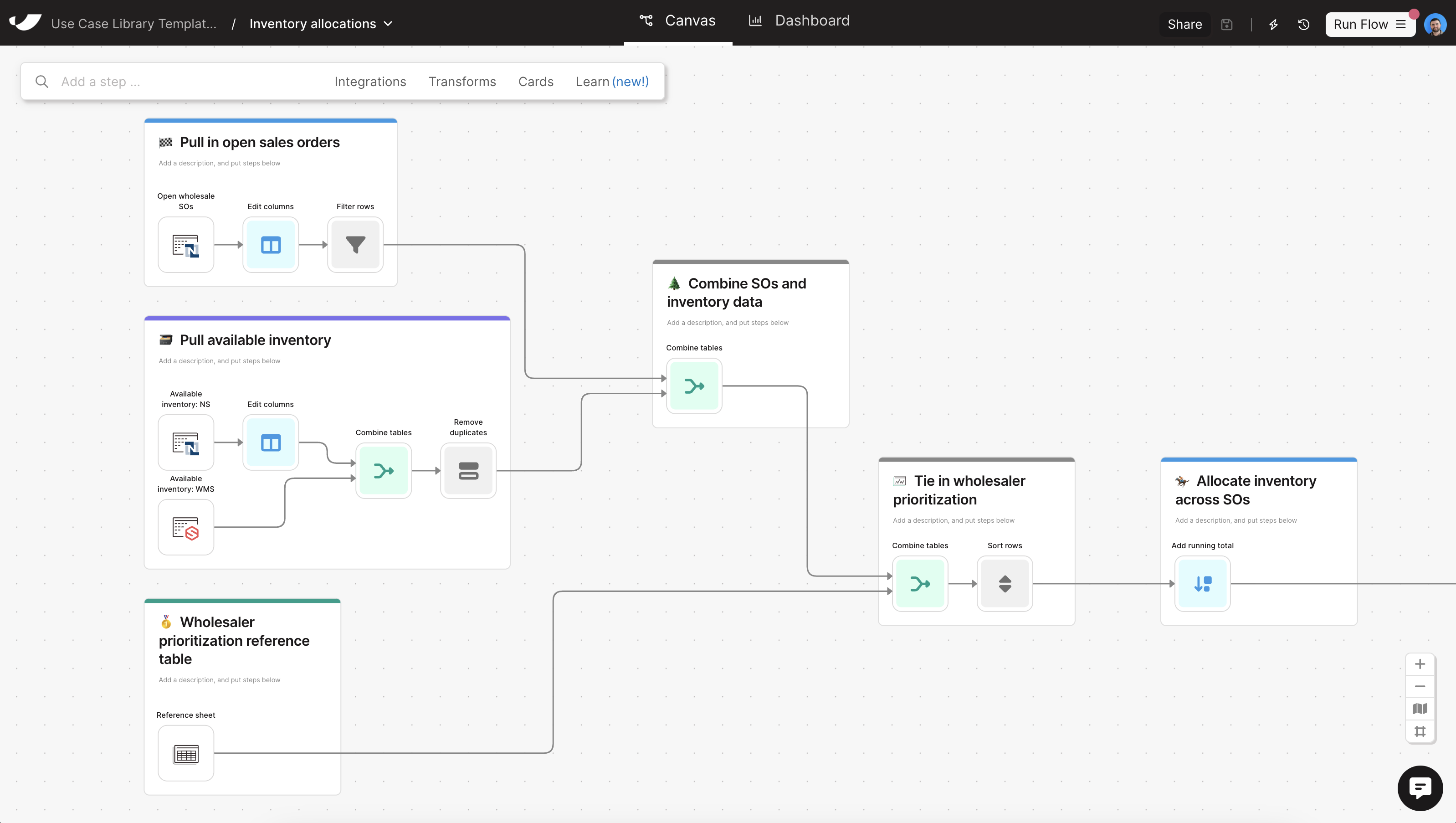
How to optimize inventory allocation across wholesalers
In order to optimize fill rates and maintain strong wholesaler relationships, it’s crucial to have visibility into available inventory and sales orders across wholesalers. For brands with large wholesaler networks, this quickly becomes complex when teams need to join data across inventory systems, demand forecasts, open sales orders, and historical sales reports just to understand how to allocate across sales orders. Add multiple product categories into the equation and the process quickly becomes a massive resource drain — resulting in missed revenue and sub-optimal fill rates.
Parabola automates inventory allocations by providing real-time visibility into open sales orders and available inventory before systematically prioritizing wholesaler SOs. Dynamically allocate inventory to improve fill rates with key wholesalers before allocating remaining stock across secondary partners to maximize profitability.
Video overview
Why Parabola
Automating inventory management in Parabola has been a huge unlock for growing our business. We can finally keep up with demand and plan for future growth.
Inventory allocation is the process of distributing available stock across multiple sales orders or channels based on priority. For wholesalers, this means ensuring key partners receive their orders first to maintain service levels and avoid stock imbalances. This process typically requires balancing inventory levels, demand forecasts, and sales orders to ensure the most efficient distribution of stock.
- Pull inventory, open sales orders, and demand forecast data from your ERP, WMS, or sales channels using steps like Pull from Netsuite and Pull from API.
- Clean your datasets, removing unnecessary columns and creating clean identifiers, using steps like Edit columns, Extract with AI, and Filter rows.
- Use the Add if/else column step or Create a Sheet to tell the Flow how to prioritize wholesalers.
- Use steps like Add math column, Sum by group, and Add running total to distribute stock based on prioritization rules.
- Push allocations back to systems like your ERP or OMS using steps like Send to API or Send to Google Sheets.
- Consider using the Create a sheet step to build a prioritization reference table for wholesalers and product categories.
- Regularly update demand forecasts to refine allocation logic and prevent over- or under-allocation.
- Use a Filter rows step to isolate sales orders exceeding available inventory and trigger alerts for partial fulfillment.
- Monitor fill rates dynamically by pushing allocated vs. requested quantities into a Parabola Table for visibility.
- To start building your own inventory allocation Flow, check out Parabola University.